Scope
Thoroughly air seal HVAC ducts to ensure delivery of all air from a home’s central HVAC air handler to the supply grille terminations without air leakage. For aerosol spray sealant applications, follow the directions of the system supplier; typically this work will be done by a factory-authorized technician. For manual duct sealing of portions of the duct system not treated by the injected spray sealant system, follow the scope described below.
Contractor Requirements
Rebuild or repair all supply and return (if any) ducts using compatible materials to prevent air leakage according to the following procedure and in compliance with all manufacturer instructions:
- For retrofits, sealing/replacement will be limited to areas that are accessible without removing/breaching gypsum wall or ceiling boards.
- For new or existing ducts, determine type of ducts in the home.
- Gain access to the joints and duct connections that will not be treated by the injected spray sealant system, including:
- plenum connections
- air-handler cabinet to plenum
- plenum to take-off connections
- boot to duct connections
- boot- to-floor/ceiling connections.
- Prepare ducts/connections for sealing. For mastic or tape-based sealant, prepare the surface for work according to product specifications (e.g., remove old tape, oil, and debris) in order to receive new sealant.
- Seal all accessible ducts/connections listed above with:
- pliable, water-based sealant labeled as meeting UL-181 standards, or
- foil or mastic HVAC tape labeled as meeting UL-181 standards, and
- boot- to- floor/ceiling connections shall be sealed with silicone caulking, pliable mastic or other sealant
- Replace damaged ducts or sections of ducts where it is more cost effective to replace than repair and air seal.
- Repair or replace duct insulation as needed where accessible. New duct insulation shall be R-8. Repaired or replaced duct insulation shall have a complete vapor retarder.
- Clean up all debris from duct sealing and replace any disturbed insulation.
- Clean any work-related debris, dirt, dust, etc. from within the living space.
See the Compliance Tab for links to related codes and standards and voluntary federal energy-efficiency program requirements.
Description
Air-tight ductwork is important to prevent energy loss, provide comfort, and avoid unwanted pressure imbalances that can result from air leaking outside a home’s thermal envelope. Ideally, all air moved by the air handler should arrive at the supply grille terminations without air leakage, and all air entering the return duct grilles should arrive back at the air handler without leakage. Duct sealing is important for new construction and older homes. Often older duct systems are quite leaky. Remedial duct sealing can dramatically improve the performance of a home’s HVAC system.
Duct sealing with an injected aerosolized acrylic sealant is an effective way to eliminate duct leakage, when combined with manual sealing of other easily accessible areas. Other retrofit products for sealing ducts from the inside include commercially available spray-on coating products.
The acrylic sealant is injected into pressurized supply and return ducts. Sealant particles accumulate at leakage locations, gradually closing the leak. Gaps larger than 5/8 in. are recommended to be sealed manually with fiberglass mesh tape and mastic, and the duct material must have an interior air barrier. See more information about the aerosolized acrylic sealant process. The injection system continuously measures airflow and leakage throughout the sealing process and the process is halted when the leakage has been reduced to the desired level. The connections from the duct system to the air handler as well as to registers are blocked off to prevent the sealant from fouling HVAC equipment or escaping into the living space.
The sealant injection system will typically measure total duct leakage of the system that the sealant is treating; however, in order to measure duct leakage to the outside for the entire system (including air handler, returns, and at registers) a separate duct leakage test would need to be conducted.
The spray sealant system treats the ductwork; however, because the registers and air handler are blocked off, it does not seal leaks in the return, air handler, or at the junction between registers and finish surfaces (wall/ceiling/floor). These areas must be sealed by hand, which is possible because they are usually accessible.
Injected spray sealant is less suitable for sealing systems to less than 40 to 60 CFM of leakage. A minimum airflow speed is necessary to keep the sealant suspended in the airstream. When leakage gets below 40 to 60 CFM, the flow becomes too low and the system may no longer function properly.
High ambient relative humidity also complicates application. The sealant needs to enter the duct system “dry”; i.e., a skin should form around each droplet of sealant. This is accomplished by passing the sealant through a heated 8 to 10 ft. plastic tunnel prior to entry into the duct system. Under humid conditions, the sealant needs more time in the tunnel to dry out, requiring slower airflow or a longer tunnel.
Connecting the sealant injection system to supply ductwork can be challenging for small homes or cramped areas, or where clearance between the top of the air handler heating coil and the ceiling is small. In some cases, a portion of the equipment may need to be placed out of doors, which can be difficult in inclement weather.
Isolating the space conditioning equipment from the duct system is crucial to avoiding damage to that equipment. At times, this can be a challenge. Finally, whenever technology replaces manual methods, the possibility of equipment failure arises that can delay or halt a job.
Materials
The vendors of the injected spray sealant system will provide all equipment and materials necessary for its use; however, the following additional materials are needed for the manual sealing portion of the project:
- pliable, water-based sealant labeled as meeting UL-181 standards, or
- foil or mastic HVAC tape labeled as meeting UL-181 standards, and
- silicone caulk
- fiberglass mesh tape to reinforce mastic for large gaps
- rags and cleaning supplies to remove dirt and dust from duct surfaces to be sealed
- hand tools for removing and replacing register covers.
Who Does the Work
Most local codes will require a licensed HVAC contractor to perform this work.
How-to Seal Ducts with an Injected Spray System
Note steps involving the spray sealant injection system will be conducted by a factory-authorized installer.
Assemble the spray sealant injection system.
Figure 1. A technician assembles the spray sealant injection system to seal HVAC ducts from the inside. (Source: ARIES.) Block off registers so sealant does not enter living space. The air handler connection to the supply and return ducts must also be blocked off to prevent sealant from fouling the mechanical equipment.
Figure 2. Block off registers before installing spray sealant in HVAC ducts. (Source: ARIES.) Connect the plastic application tunnel from the injection equipment (Figure 3) to the supply plenum (Figure 4). The assembled injection system includes a blower/heater-background, and the sealant injection unit-foreground (Figure 5).
Figure 3. Connect the plastic application tunnel to the injection equipment. (Source: ARIES.) Figure 4. Connect the plastic application tunnel from the injection equipment to the supply plenum. (Source: ARIES.) Figure 5. The duct sealing spray injection system includes a blower/heater (background) and the sealant injection unit (foreground). (Source: ARIES.) Turn on the spray injection system. The tunnel inflates as the injection system operates. Software tracks the sealing progress and controls the airflow.
Figure 6. The duct sealing spray injection system application tunnel inflates as the injection system operates. (Source: ARIES.) - Perform additional manual sealing. (These steps can be done by the vendor technician or other trades selected by the builder.) Seal around the opening to the supply plenum, seams in the return plenum, around the registers, and seams in the air handler box with mastic and/or foil tape.
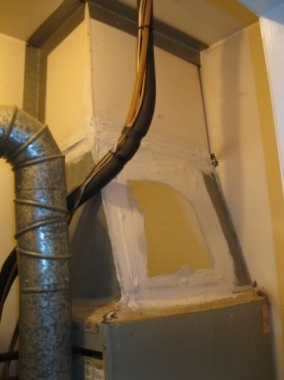
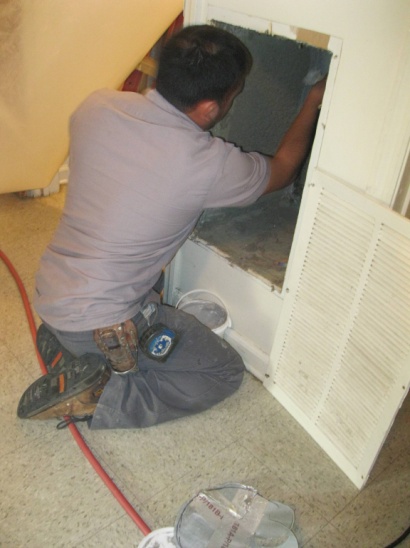
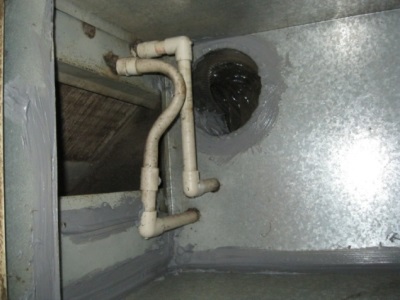
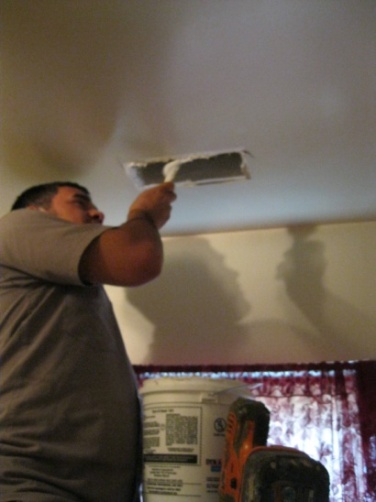
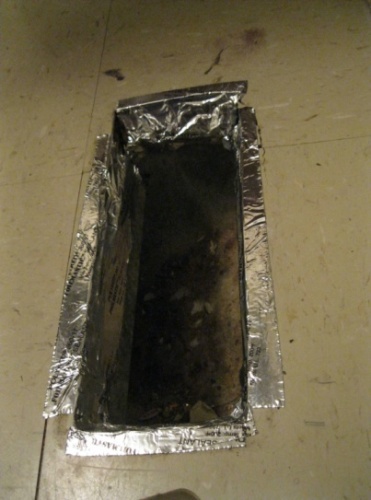
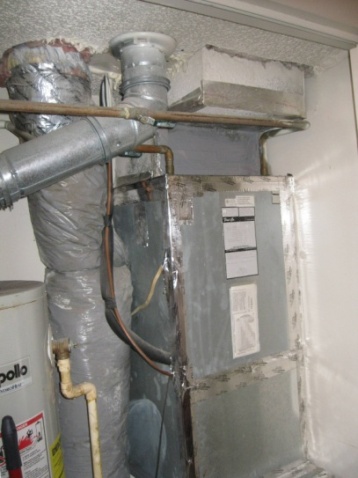
Success
Before and after sealing, duct leakage testing can be used to verify proper implementation and quantify the improvement. If the system was extremely leaky, duct sealing may result in significantly greater volumes of air being delivered to spaces. Rebalancing of the system is recommended in these cases so as not to over-heat or over-cool rooms.
Usually duct sealing will reduce the risk of combustion safety problems such as back-drafting; however, the effects of duct sealing on combustion appliances and venting should be tested to confirm the tighter ducts do not negatively alter the pressure dynamics of the home to create such problems.
Climate
Ducts should be sealed in all climate zones. The more extreme the climate (either hot or cold) the greater the benefit from duct sealing will be realized.
Training
Compliance
More
More Info.
Access to some references may require purchase from the publisher. While we continually update our database, links may have changed since posting. Please contact our webmaster if you find broken links.
The following authors and organizations contributed to the content in this Guide.
The Levy Partnership, Inc., lead for the ARIES Collaborative, a DOE Building America Research Team
Sales
Tight Duct Sealing =
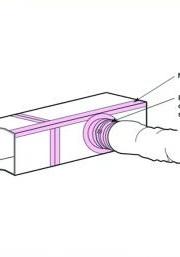
As conditioned air flows from heating and cooling equipment to the spaces where people live, excessive leaks compromise comfort, health, and durability while increasing energy costs. This is because conditioned air escapes ducts supplying heating and cooling, and potentially contaminated air is pulled into the ducts, returning air to the heating and cooling equipment. Professionally sealed comfort delivery systems are significantly air-tight at all seams and connections. Sealing helps conditioned air get where it is needed, at the correct temperature, without pulling in contaminants from crawlspaces and attics.