Scope
Air seal the floor above a garage when there is living space above the garage and make sure floor insulation is in full contact with the underside of the subfloor.
- Seal all seams, gaps, and holes in the subfloor air barrier with caulk or foam.
- Air seal rim joists and any holes in the top plate of the garage walls.
- Install insulation without misalignments, compressions, gaps, or voids.
- Install supports to keep insulation in permanent contact with the air barrier above, for example, metal staves for batt insulation or netting for blown insulation.
- If spray foam insulation is used for the floor cavity insulation, the spray foam can serve as the air barrier if it is at least 5.5 inches thick if open-cell or at least 1.5 inches thick if closed-cell spray foam insulation.
- Consider a combination of spray foam and fibrous insulation to thoroughly air seal and meet insulation R-value requirements.
See the Compliance Tab for related codes and standards requirements, and criteria to meet national programs such as DOE’s Zero Energy Ready Home program, ENERGY STAR Single-Family New Homes, and Indoor airPLUS.
Description
Even when a garage is attached to the home, it is still outside the thermal envelope of the home, so the walls and ceiling separating it from the rest of the home must be insulated and air sealed just like any exterior walls or floors above unconditioned space. For the Insulation installed in the floor above a garage to be effective, it must be in full contact (continuous alignment) with the subfloor above and with the rim joists on all sides and any seams or holes in the subfloor and rim joists must be sealed. This air sealing provides a continuous air barrier which serves two purposes: it keeps wind from blowing through the insulation and robbing it of its thermal value and, even more importantly, it prevents garage air pollutants like car exhaust and chemical fumes from migrating into the home (EPA 2008).
When the insulation is not in contact with the subfloor (as shown in Figure 1), it creates space for air to flow, either from unsealed exterior walls or from convective loops of air currents. The moving air pulls heat from the floor system, robbing the insulation of its effectiveness and causing cold floors above. The solution to eliminating these thermal short circuits is two-fold: First, completely air seal the floor system, paying particular attention to sealing the band/rim joist area to create a continuous air barrier. Second, install the ceiling insulation in full alignment (continuous contact) with this air barrier (EPA 2008).


How to Insulate and Air Seal the Floor above an Attached Garage
- Install a subfloor that can serve as a continuous air barrier between the garage and the rooms above. In most cases, this air barrier will be plywood or OSB floor sheathing. Install the subfloor sheathing panels according to APA Sturd-I-Floor recommendations, which includes the following (APA 2011):
- Install subfloor in panel widths that align with the framing (typically 16-, 20-, or 24-inches on-center).
- Stagger subfloor panel end joints.
- Use tongue-and-groove subfloor panels or install blocking beneath panel joints.
- Apply construction adhesive or caulk at panel seams and between subfloor panel and framing members.
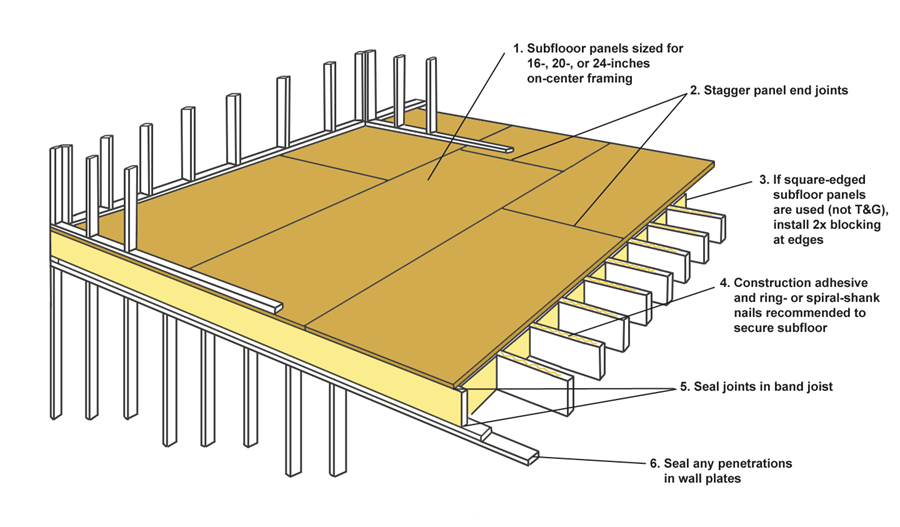
- Air seal the band and rim joists and any penetrations.
- Block off any open floor joists running from the garage ceiling to under other parts of the home to prevent the infiltration of airborne pollutants (EPA 2008). See the guide Garage Rim/Band Joist Adjoining Conditioned Space for more information. Use an air barrier material such as plywood, sheathing, rigid foam, or OSB (see Figure 4). Do not use batt insulation for air sealing.
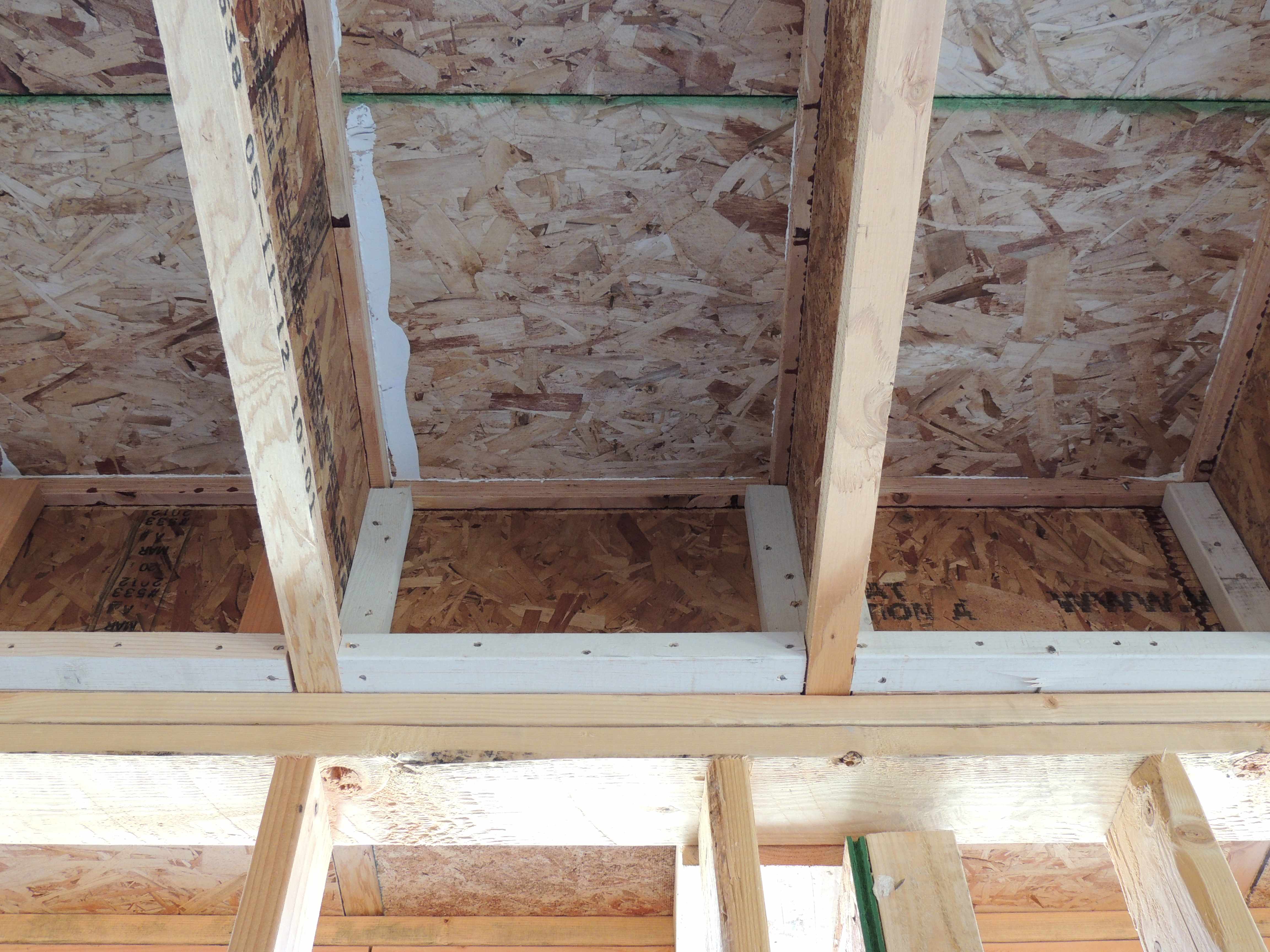
- If I-joists are used, the blocking material must be cut to fit the shape. This can be done with filler strips as shown in Figure 4. Or, the corners of the blocking may be cut to fit around the I-joist flanges, as shown in Figure 5.
- Seal the edges of the blocking with a one- or two-part foam sealant or caulk. Foam sealant will work better (and last longer) than caulk. Spray foam can be used to cover the whole air barrier (Figure 6) to fill small voids and cracks to effectively stop air flow, while also providing additional R-value (DOE 2012).


- Install insulation in the floor joists.
- Insulation should be fully "aligned" with the air barrier, i.e., in full contact with the subfloor above. There can be no gaps between the insulation and the sheathing above it (EPA 2011).
- Batt insulation should fit tightly between the floor joists but avoid gaps, compressions, or voids. Batts should be fully lofted (not crammed or compressed into the space, see Figure 7). Batts should be cut lengthwise to fit narrow joist bays, and split to fit neatly around electrical wiring running across joist bays. See the guide Insulation Installation Achieves RESNET Grade 1 for more on quality installation.

- Blown-in fiberglass or cellulose is especially effective for insulating garage ceilings when webbed floor trusses are used because it can fill in voids around the trusses. First install netting or the ceiling drywall to hold the insulation. Install the blown-in insulation to the correct volume and density to maintain contact with the subfloor above and prevent settling. Confirm with the insulation manufacturer or installer that the drywall will hold the weight of the insulation needed (EPA 2008).
- Spray foam insulation can be used to insulate the floor above a garage as well as the band joist. Spray foam provides high R-value and a continuous air barrier in one labor-saving application. To qualify as an air barrier, open-cell spray foam must have a finished thickness ≥ 5.5 inches and closed-cell spray foam must have a finished thickness ≥ 1.5 inches (EPA 2011).
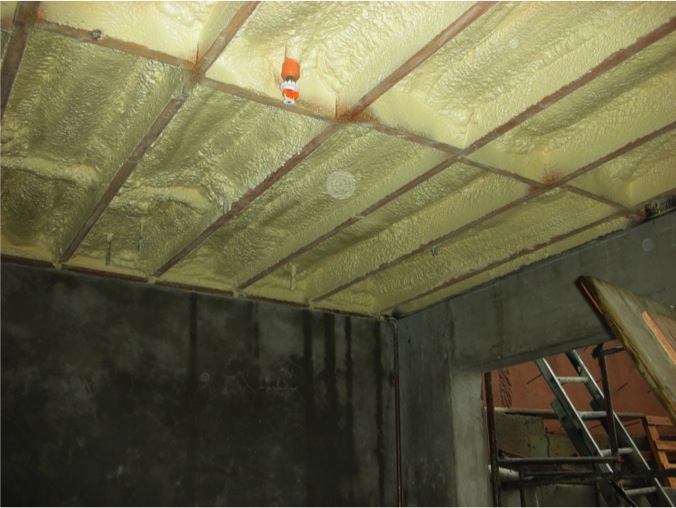
- Support insulation.
- Batt insulation must be installed to sufficient depth that it will stay in contact with the subfloor above when drywall is installed below it. If drywall will not be installed, install metal staves or mechanically fastened wire to keep batts in continuous contact with the subfloor above.
- Blown insulation must be installed at sufficient depth and density to completely fill the floor joist cavities from the ceiling drywall to the subfloor above.
- Spray foam alone requires no additional support. If spray foam is used in combination with batt or blown insulation, the batt or blown insulation must be supported or installed at sufficient depth to fill the ceiling cavities.

Success
Blower door testing conducted as part of whole-house energy performance testing, may help indicate whether air leakage at the floor has been successfully sealed. Infrared imaging with an infrared camera may be used to determine air leakage at the floor over a garage. For best results, scan twice. First, scan under static conditions before blower door testing has been conducted. This will allow the technician to evaluate the integrity of insulation behind the drywall if the garage ceiling has been finished. Conduct a second scan with the blower door running in depressurization mode and the door between the house and the garage open. This will demonstrate the integrity of the air barrier, showing where air leakage has infiltrated the framing and seeped through insulation. With the blower door pressurizing, the garage door closed and the door to the house open, check for air leaks in the floor and near the rim joist with a smoke pencil. A smoke trail moving away from the smoke pencil indicates a leak to the unconditioned space that should be sealed.
Climate
In cold climates, avoid installing plumbing in floors over garages because the pipes could freeze.
Install insulation in amounts that meet or exceed code-required levels for your climate zone.
The map in Figure 1 shows the climate zones for states that have adopted energy codes equivalent to the International Energy Conservation Code (IECC) 2009, 12, 15, and 18. The map in Figure 2 shows the climate zones for states that have adopted energy codes equivalent to the IECC 2021. Climate zone-specific requirements specified in the IECC are shown in the Compliance Tab of this guide.
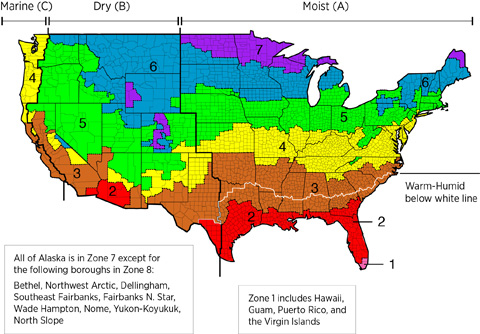
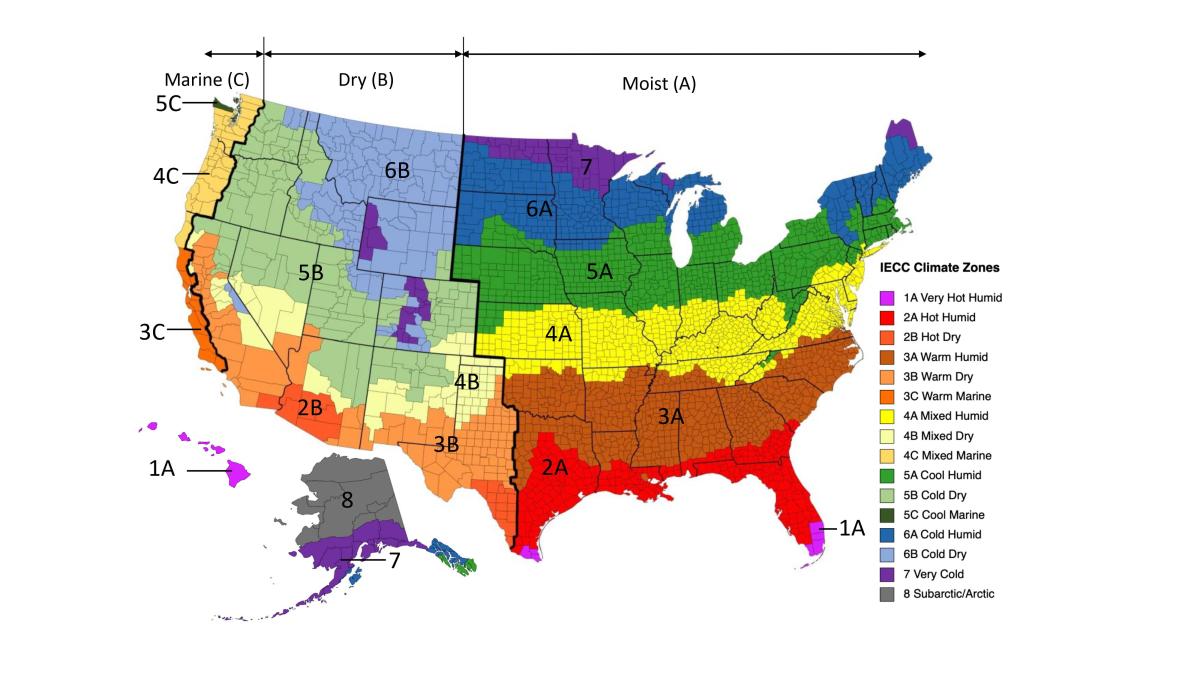
Training
CAD
Compliance
Compliance
The Compliance tab contains both program and code information. Code language is excerpted and summarized below. For exact code language, refer to the applicable code, which may require purchase from the publisher. While we continually update our database, links may have changed since posting. Please contact our webmaster if you find broken links.
ENERGY STAR Single-Family New Homes, Version 3/3.1 (Rev. 11)
National Rater Field Checklist
Thermal Enclosure System.
2. Fully-Aligned Air Barriers.7 At each insulated location below, a complete air barrier is provided that is fully aligned as follows:
Floors: At exterior vertical surface of floor insulation in all climate zones and, if over unconditioned space, also at interior horizontal surface including supports to ensure alignment. Alternatives in Footnotes 12 & 13.11, 12, 13
2.6 Floors above garages, floors above unconditioned basements or crawlspaces, and cantilevered floors.
Footnote 7) For purposes of this Checklist, an air barrier is defined as any durable solid material that blocks air flow between conditioned space and unconditioned space, including necessary sealing to block excessive air flow at edges and seams and adequate support to resist positive and negative pressures without displacement or damage. EPA recommends, but does not require, rigid air barriers. Open-cell or closed-cell foam shall have a finished thickness ≥ 5.5 in. or 1.5 in., respectively, to qualify as an air barrier unless the manufacturer indicates otherwise. If flexible air barriers such as house wrap are used, they shall be fully sealed at all seams and edges and supported using fasteners with caps or heads ≥ 1 in. diameter unless otherwise indicated by the manufacturer. Flexible air barriers shall not be made of kraft paper, paper-based products, or other materials that are easily torn. If polyethylene is used, its thickness shall be ≥ 6 mil.
Footnote 11) EPA highly recommends, but does not require, an air barrier at the interior vertical surface of floor insulation in Climate Zones 4-8.
Footnote 12) Examples of supports necessary for permanent contact include staves for batt insulation or netting for blown-in insulation. Alternatively, supports are not required if batts fill the full depth of the floor cavity, even when compression occurs due to excess insulation, as long as the R-value of the batts has been appropriately assessed based on manufacturer guidance and the only defect preventing the insulation from achieving the required installation grade is the compression caused by the excess insulation.
Footnote 13) Alternatively, an air barrier is permitted to be installed at the exterior horizontal surface of the floor insulation if the insulation is installed in contact with this air barrier, the exterior vertical surfaces of the floor cavity are also insulated, and air barriers are included at the exterior vertical surfaces of this insulation.
Please see the ENERGY STAR Single-Family New Homes Implementation Timeline for the program version and revision currently applicable in your state.
DOE Zero Energy Ready Home (Revision 07)
Exhibit 1 Mandatory Requirements.
Exhibit 1, Item 1) Certified under the ENERGY STAR Qualified Homes Program or the ENERGY STAR Multifamily New Construction Program.
Exhibit 1, Item 2) Ceiling, wall, floor, and slab insulation shall meet or exceed 2015 IECC levels and achieve Grade 1 installation, per RESNET standards. See the guide 2015 IECC Code Level Insulation – DOE Zero Energy Ready Home Requirements for more details.
Exhibit 2 DOE Zero Energy Ready Home Target Home.
The U.S. Department of Energy’s Zero Energy Ready Home program allows builders to choose a prescriptive or performance path. The DOE Zero Energy Ready Home prescriptive path requires builders to meet or exceed the minimum HVAC efficiencies listed in Exhibit 2 of the National Program Requirements (Rev 07), as shown below. The DOE Zero Energy Ready Home performance path allows builders to select a custom combination of measures for each home that is equivalent in performance to the minimum HERS index of a modeled target home that meets the requirements of Exhibit 2 as well as the mandatory requirements of Zero Energy Ready Home Exhibit 1.
Exhibit 2, Insulation and Infiltration) Insulation levels shall meet the 2015 IECC and achieve Grade 1 installation, per RESNET standards. Whole house leakage must be tested and meet the following infiltration limits:
- Zones 1-2: ≤ 3 ACH50;
- Zones 3-4: ≤ 2.5 ACH50;
- Zones 5-7: ≤ 2 ACH50;
- Zone 8: ≤ 1.5 ACH50;
- Attached dwellings: ≤ 3 ACH50.
Footnote 13) Steel-frame ceilings, walls, and floors shall meet the insulation requirements of the 2015 IECC – Table 402.2.6.
Footnote 23) Envelope leakage shall be determined by an approved verifier using a RESNET-approved testing protocol.
2009-2021 IECC and IRC Insulation Requirements Table
The minimum insulation requirements for ceilings, walls, floors, and foundations in new homes, as listed in the 2009, 2012, 2015, 2018, and 2021 IECC and IRC, can be found in this table.
2009, 2012, 2015, 2018, and 2021 International Energy Code (IECC)
Table R402.4.1.1 Air Barrier and Insulation Installation, Floors: Insulation in floors (including above garage and cantilevered floors) is installed to maintain permanent contact with underside of subfloor decking. A continuous air barrier is installed in the building envelope including rim joists and exposed edges of insulation. Breaks or joints in the air barrier are sealed. Air permeable insulation is not used as a sealing material. Junction of foundation and wall sill plates, wall top plate and top of wall, sill plate and rim-band, and rim band and subfloor are sealed. Corners, headers, and rim joists making up the thermal envelope are insulated.
Table R402.1.1 (Table R402.1.2 in 2015 and 2018 IECC) Insulation and Fenestration Requirements – meet or exceed the insulation levels listed in this table.
Retrofit: 2009, 2012, 2015, 2018, and 2021 IECC
Section R101.4.3 (in 2009 and 2012). Additions, alterations, renovations, or repairs shall conform to the provisions of this code, without requiring the unaltered portions of the existing building to comply with this code. (See code for additional requirements and exceptions.)
Chapter 5 (in 2015, 2018, 2021). The provisions of this chapter shall control the alteration, repair, addition, and change of occupancy of existing buildings and structures.
2009, 2012, 2015, 2018 IRC, and 2021 International Residential Code (IRC)
Table N1102.4.1.1 Air Barrier and Insulation Installation, Floors: Insulation in floors (including above garage and cantilevered floors) is installed to maintain permanent contact with underside of subfloor decking. A continuous air barrier is installed in the building envelope including rim joists and exposed edges of insulation. Breaks or joints in the air barrier are sealed. Air permeable insulation is not used as a sealing material. Junction of foundation and wall sill plates, wall top plate and top of wall, sill plate and rim-band, and rim band and subfloor are sealed. Corners, headers, and rim joists making up the thermal envelope are insulated.
Table N1102.1.1 (Table N1102.1.2 in 2015, 2018, and 2021 IRC) Insulation and Fenestration Requirements – meet or exceed the insulation levels listed in this table.
Retrofit: 2009, 2012, 2015, 2018, and 2021 IRC
Section R102.7.1 Additions, alterations, or repairs. Additions, alterations, renovations, or repairs shall conform to the provisions of this code, without requiring the unaltered portions of the existing building to comply with the requirements of this code, unless otherwise stated. (See code for additional requirements and exceptions.)
Appendix J regulates the repair, renovation, alteration, and reconstruction of existing buildings and is intended to encourage their continued safe use.
More
More Info.
Access to some references may require purchase from the publisher. While we continually update our database, links may have changed since posting. Please contact our webmaster if you find broken links.
The following authors and organizations contributed to the content in this Guide.
Pacific Northwest National Laboratory
Building Science Corporation, lead for the Building Science Consortium (BSC), a DOE Building America Research Team
Sales
Fully Aligned Air Barriers = Whole-House Draft Barrier

A whole-house draft barrier is a continuous layer of air-tight materials that block air leaks. This barrier can be integrated with other materials to also function as a water barrier, thermal barrier, and vapor barrier. For example, rigid foam insulation can be used to block thermal flow as well as air flow when seams are sealed with tape, caulk, adhesives, or liquid-applied sealants. Some rigid foams have an integrated water control layer as well. Additionally, drywall can serve as an interior air barrier when the seams are taped and spackled, and caulk, spray foam, or gaskets are used to seal around wiring, plumbing, and other penetrations. It also serves as the vapor barrier when finished with paint. Insulation should be in full contact with the air barrier layer.